Spray Foam vs. Blown-In Fiberglass Insulation
December 22nd, 2023
5 min read
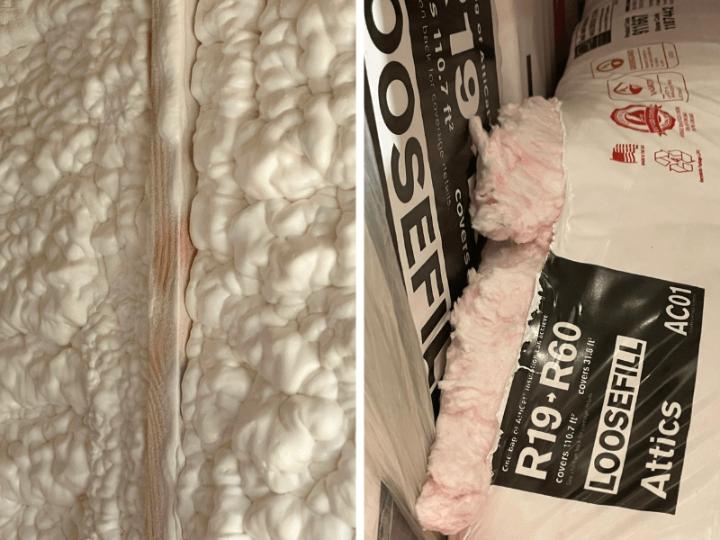
You're on a budget but want as much insulation efficiency as you can manage. Is blown-in fiberglass the low-cost solution for your project? Or does your home need the high-performance of spray foam insulation?
South Central Services has installed spray foam insulation in hundreds of homes in and around Greencastle, Pennsylvania. We speak with interested homeowners weekly about their insulation needs and help them determine the best solution. The specifics of your project will determine which insulation is best for you.
By the end of this article, you will know:
- What spray foam and blown-in fiberglass insulation are made of
- Where spray foam and blown-in fiberglass insulation can be installed
- What features spray foam and blown-in fiberglass insulation offer
Don't have time to read right now? Check out everything you need to know at a glance.
What Are Spray Foam and Blown-In Fiberglass Made Of?
Spray polyurethane foam (SPF) is a polyurethane foam insulation. Two chemical components react to create spray foam. The chemicals are heated, pressurized, and then mixed. The exothermic reaction results in plastic foam.
Fiberglass insulation is made of fine glass and plastic fibers. The three most common formats for fiberglass insulation are batts, blankets, and loose-fill.
Blown-in fiberglass is the process of blowing loose-fill fiberglass into cavities.
Where Can Spray Foam and Blown-In Fiberglass Be Installed?
Spray foam and blown-in fiberglass have different application options. One insulation is quite versatile, while another is best suited for a single application. Let's examine the versatility of these insulations in more detail.
Spray Foam Insulation Can Be Installed Anywhere.
There are two kinds of spray foam: open cell and closed cell. Where the foam can be installed will depend on the type of foam.
Open cell foam is a low-density, above-grade product. Above-grade refers to places that are above ground, like attics. Other above-grade applications could include some exterior walls and in-between floors. Open cell foam can also fill open cavities and create a sound barrier.
In most cases, if open cell foam can be installed, closed cell foam could also be installed. Closed cell foam is appropriate in above- and below-grade applications.
The higher density of closed cell foam allows it to create a vapor barrier at 2 inches of thickness. Basements, crawl spaces, and foundation slabs are places where closed cell foam can be used underground.
Blown-In Fiberglass Insulation Is Best Installed On Attic Floors.
Blown-in fiberglass insulation is best installed in attics. Due to its loose-fill nature, blown-in fiberglass has limited applications.
Fiberglass is also not a product for below-grade applications. Crawl spaces and basements have increased moisture content from being underground.
What Features Do Spray Foam and Blown-In Fiberglass Offer?
How do spray foam and blown-in fiberglass compare from feature to feature? Here's a preview of several insulation features that we'll compare in this article.
- Energy efficiency
- Fire resistance
- Mold resistance
- Ease of installation
- Price
- Product lifetime
Let’s examine each of these topics in more detail.
1. Spray Foam Offers An Airtight Seal, Which Delivers More Energy Efficiency.
The main culprit of high energy bills is often uncontrolled air exchange. Air infiltration and exfiltration allows air to flow freely through gaps in building construction. The air brings temperature fluctuations with it. By creating an airtight seal, spray foam insulation can prevent this form of energy loss.
Homeowners generally see a 30% to 70% decrease in their energy bills after insulating with spray foam, depending on what insulation it replaced.
Fiberglass insulation does not create an airtight seal, so its energy efficiency performance cannot compare to spray foam. The design of fiberglass allows for airflow, trying to slow heat transfer through air travel. Fiberglass insulation is prone to air leakage.
Blown-in fiberglass attempts energy efficiency by filling cracks and crevices. However, if not paired with a separate air-sealing product, blown-in fiberglass cannot offer significant measurable decreases in energy bills.
2. Both Spray Foam And Blown-In Fiberglass Are Fire Resistant.
Spray foam is a combustible material with a Class 1 fire rating. Combustible materials with this rating can eventually melt or burn but pass flame spread and smoke development tests. These tests evaluate how long it takes for a material to catch fire or create smoke.
By adding fire retardant to the spray foam formula, spray foam insulation can pass smoke development and flame spread tests. Manufacturers add flame retardant to the spray foam formula during development.
As for fiberglass, it is a noncombustible material. Blown-in fiberglass has a Class 1 fire rating since it is a noncombustible material. Noncombustible materials do not burn or melt if exposed to fire.
3. Both Are Mold Resistant On Paper, But Must Be Installed Correctly.
Closed cell spray foam creates a vapor barrier at a depth of 2 inches. By preventing the moisture in the air from passing through the foam, the vapor barrier can mitigate the chances of mold. Vapor barriers do not prevent mold in every scenario, but the plastic of spray foam does not promote mold growth.
No matter the depth of open cell insulation, its open cell structure will not create a vapor barrier. This limitation is why open cell spray foam is limited to above-grade applications. Above-grade applications can still experience moisture, but above-grade installations of open cell foam should not grow mold if installed correctly.
Blown-in fiberglass is technically a mold-resistant insulation, as plastic and glass are mold-resistant materials. However, humidity and moisture can travel with air passing through fiberglass insulation. The insulation and its surroundings can grow mold if blown-in fiberglass is installed incorrectly.
4. Blown-In Fiberglass Is Easier To Install Than Spray Foam Insulation.
Professional contractors must install spray foam insulation. While you can find DIY spray foam kits available for purchase, we do not recommend these kits for homeowners. Spray foam is a product that is manufactured on-site using raw chemicals and expensive equipment.
Installers must monitor these chemicals for safe and effective application. Contractors must also protect themselves with suits and respirators while on the job. When spray foam is being installed, residents and pets are asked to vacate for their safety.
Meanwhile, either a handy homeowner or an insulation contractor can install blown-in fiberglass insulation. Many homeowners opt to install blown-in fiberglass DIY in an attempt to save money.
Installing blown-in fiberglass yourself will require some math. To install effective insulation, the amount of insulation must meet the R-value of the project. The required R-value will vary by building codes and climate zone.
DIY blown-in insulation also requires equipment rental and personal protective equipment (PPE). Blowing machines are generally available for rent from rental companies or home improvement stores. Safety glasses, gloves, and a mask are necessary to prevent glass fibers from lodging in your skin, lungs, and eyes.
5. Spray Foam Is More Expensive Than Blown-In Fiberglass.
Closed cell spray foam is more expensive than open cell spray foam. Price will also vary by the depth of foam that must be sprayed. Homeowners can expect to pay between $4 and $9 per square foot for spray foam insulation.
Handy homeowners who install fiberglass themselves will pay approximately $2 per square foot for the materials. Equipment rental will also factor into this price.
Hiring a contractor to install blown-in fiberglass insulation for you will increase the price due to man-hours and other factors.
6. Spray Foam Insulation Lasts Longer Than Blown-In Fiberglass.
The lifetime of undisturbed spray foam insulation is indefinite. Only exposure to UV rays can deteriorate stable spray foam insulation. Inside a structure, spray foam insulation can be a permanent solution. Outside of a structure, spray foam requires additional coatings since it will be exposed to sunlight.
In theory, blown-in fiberglass insulation should last between 80 and 100 years if undamaged. In real-world applications, blown-in fiberglass insulation should be checked for damages every 15 to 20 years. If the blown-in insulation is exposed to moisture, mold or mildew damage could occur.
Blown-in insulation products also settle over time. As blown-in fiberglass settles, the R-value decreases. Once the R-value dips below the necessary value for the area of the home, the insulation is no longer effective.
As long as the fiberglass is undamaged, more blown-in insulation can be installed on top of the existing insulation. However, maintaining the blown-in fiberglass will incur more costs for materials.
The Bottom Line About Blown-In Fiberglass and Spray Foam
Whether you should use spray foam or blown-in fiberglass will depend on what you want to insulate. Blown-in fiberglass has limited features and applications compared to spray foam, but may be the right budget product for your attic. If your project is below-grade, you will need closed cell spray foam insulation for its vapor barrier capabilities.
Now that you know the differences between spray foam and blown-in fiberglass, your next step is to:
- Estimate the cost of spray foam for your attic
- Weigh the pros and cons of spray foam in your attic
- Find out if blown-in insulation is better than batt insulation
Disclaimer: While we strive to publish information accurate to building science, local building codes and standards supersede our recommendations.
Alexis has been fascinated by spray foam insulation since 2018. When she isn’t thinking about insulation, Alexis is geeking out over storytelling and spreadsheets.
Topics: