Why Is Spray Foam Insulation So Expensive?
August 18th, 2023
6 min read
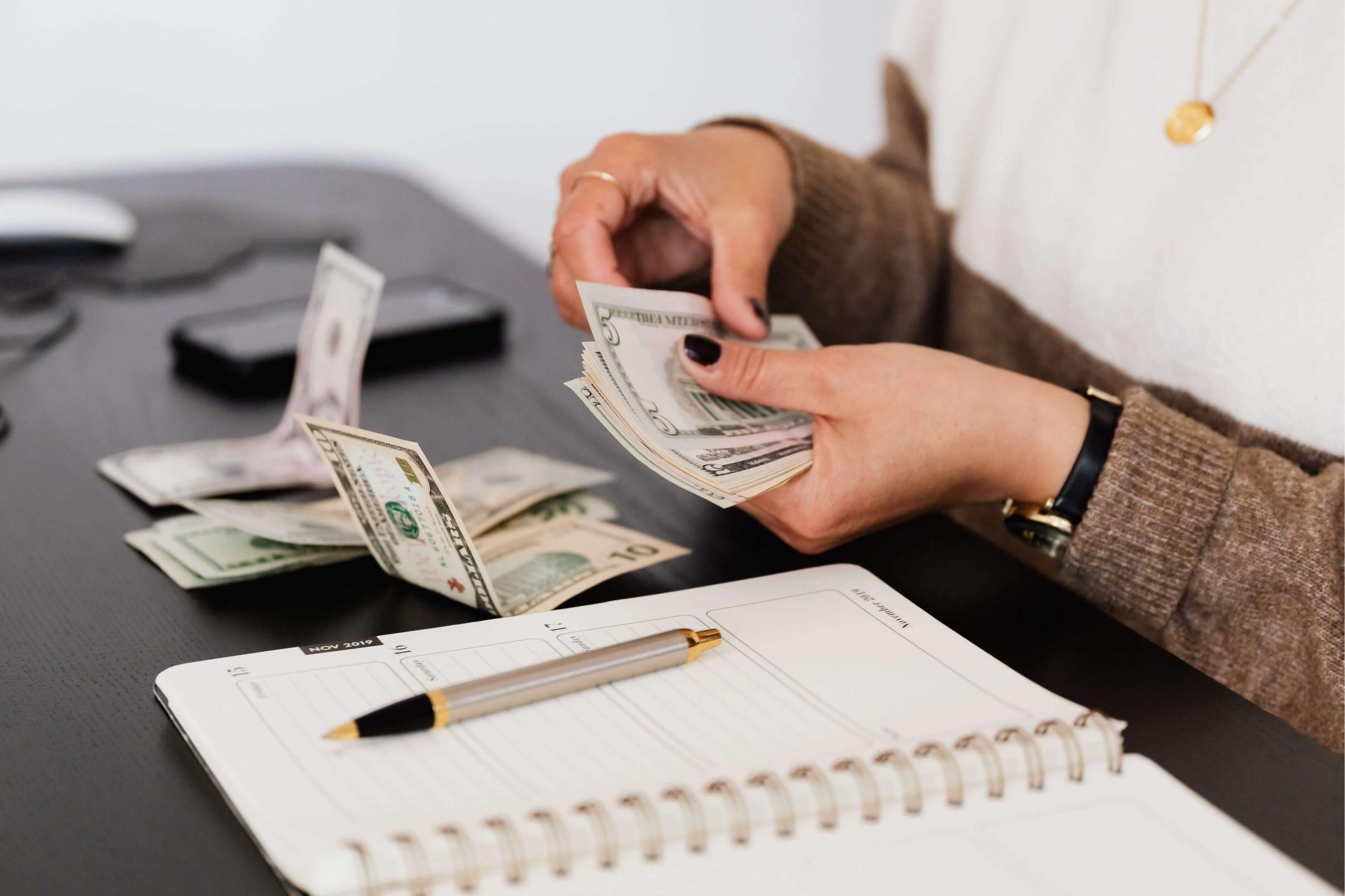
Spray foam is one of the most expensive insulation products on the market. While it may be worth the price, it's hard to justify the cost when you don't know what factors create that price. You want to understand what contributes to the hefty price tag of spray foam, and we want you to know that, too.
South Central Services has given quotes for and installed spray foam in hundreds of homes around Greencastle, Pennsylvania. This article will share all of the factors, both big and small, that impact the cost of spray foam insulation. By the end of this article, you will know:
- Why spray foam is a premium product
- The rates of spray foam insulation to install
- Every factor that could impact your quote
- What price can tell you about contractor expertise
Don't have time to read right now? Check out everything you need to know at a glance.
How Much Spray Foam Insulation Costs
When we say spray foam insulation is expensive, how costly do we mean?
At South Central Services, we charge the following rates for open and closed cell spray foam.
- Open cell spray foam insulation: $0.25 to $0.75 per board foot
- Closed cell spray foam insulation: $1.15 to $1.75 per board foot
At first glance, those prices might not seem that high. These are prices per board foot, not per square foot. After calculating the board feet of your project, spray foam insulation will seem much pricier.
Looking for a quick estimating tool? Check out our rough estimating tools for the lowest, average, and highest cost for projects like basements, attics, and crawl spaces.
Compared to other insulations, which may cost only $1 to $2 per square foot, spray foam insulation is more expensive. Spray foam's cost per square foot varies by project type and foam type.
For example, open cell in an exterior wall may cost between $2.25 and $3.38 per square foot. In an attic application, open cell may cost between $5.00 and $7.50 per square foot.
This difference is due to the quantity of foam. Different applications require different depths of foam.
3 Reasons Why Spray Foam Is A Premium Product
Spray foam is often described as a premium product. But what does that mean? Generally, spray foam is considered to be a premium insulation for these three reasons:
- Product performance
- Manufacturing costs
- Equipment
Let's break these reasons down into more detail.
1. Spray Foam Delivers Both R-Value And An Airtight Seal.
Spray foam insulation is a premium product because of its superior insulating performance. Traditional insulations, like fiberglass batts and blown-in products, are only concerned with slowing conductive heat transfer. We measure the ability to resist conductive heat through a metric called R-value.
All insulations should have a high R-value, indicating that they can slow conductive heat. However, heat also travels through the air via convection and radiation. In order to stop heat from exchanging in the air, you need an airtight seal.
There are products that can deliver an air-seal separately, such as can foam or caulking. However, spray foam insulation is able to insulate and air-seal simultaneously.
Because of its airtight seal, structures insulated with spray foam have lower energy bills, increased comfort, and improved air quality. Other insulation products cannot offer these benefits at the same rate because they lack air-sealing capabilities.
2. Spray Foam Is More Expensive And Complex To Manufacture.
The manufacturing costs of spray foam insulation are higher than those of other insulation products. The raw chemical materials are more expensive than recycled cellulose or glass fibers.
Chemical processing facilities are more expensive to build and maintain, with stricter safety protocols and testing protocols. There are fewer safety and testing costs associated with plants creating fiberglass and cellulose insulation because these industries do not manufacture chemicals.
3. Spray Foam Requires Specialized Equipment To Install Safely.
Most insulation products are manufactured, purchased, and then installed. Spray foam is both a product and a service, as it is manufactured and installed simultaneously on-site.
Manufacturing spray foam correctly requires precision and control, which starts in a spray foam rig. A spray foam rig is the truck or trailer that travels to job locations, containing all the materials and equipment necessary to safely apply foam.
Spray foam rigs are filled with expensive equipment which monitors temperature, pressure, and ratio. A quality spray foam rig can cost anywhere between $60,000 and $100,000 for a contractor to build.
7 Factors Impacting Individual Spray Foam Insulation Quotes
It's good to understand why spray foam is worth more than other insulation products. But what does that mean for your project? Is spray foam expensive because of the manufacturing costs, or are there other factors at play?
When it comes to the bids that spray foam contractors provide, there are numerous factors impacting the bottom line. These factors include:
- Quantity of raw materials
- Type of foam
- Accessibility
- Safety requirements
- Man-hours
- Travel time
- Contractor expertise
Let’s examine each of these factors to better understand how and why they influence price.
1. More Raw Materials Means A More Expensive Project.
This statement may seem like common sense. We can all understand that the more spray foam insulation you have installed, the higher the project cost will be.
However, it is important to clarify how spray foam contractors measure your spray foam. A common misconception is that spray foam contractors charge by the 55-gallon drum for insulation.
Many believe opening a spray foam drum is like opening a 2-liter bottle of soda. Soda will go flat, but spray foam components do not lose quality when opened or used. You will only be charged for a full drum if a project requires one.
Rather than charging by the drum, contractors calculate how much liquid chemical is needed to create enough foam for the project's board feet.
A board foot is the measurement insulation contractors use for pricing. A board foot is 1 foot by 1 foot by 1-inch thickness. The square footage of the space being sprayed is multiplied by the depth it has to be sprayed.
Our rates are per board foot are as follows:
- Closed cell: $1.15 to $1.75 per board foot
- Open cell: $0.25 to $0.75 per board foot
2. Closed Cell Spray Foam Is More Expensive Than Open Cell Spray Foam.
You likely noticed the rates of open cell and closed cell spray foam are different. The difference in cost is primarily because of density.
Open cell spray foam is less dense than closed cell spray foam. A 55-gallon drum of open cell will go farther than one of closed cell.
Your quote amount may be higher or lower, depending on whether your contractor recommends open or closed cell foam. The type of foam that will work best hinges on the application and the project details.
Generally speaking, open cell foam can be installed in above-grade places. These are locations above the ground like exterior walls, attics, and roofs. Closed cell foam can be installed anywhere that open cell foam can be installed.
Closed cell spray foam is the only spray foam installed below-grade. Below-grade applications are any applications that are below ground level. Generally, below-grade includes basements and crawl spaces.
3. Contractors May Charge More For Jobs With Limited Accessibility.
Have you ever been in a building that needed a giant ladder to change a lightbulb? Or, have you ever seen an entrance to a space so small that you weren't sure you could fit through the doorway?
Any structure that has accessibility issues can incur additional costs. Having to install scaffolding or provide man lifts costs time and money. Not only are there man-hours to set up these accommodations, but working with the accommodations can also slow down the work.
Crawl spaces are a classic example of limited accessibility. However, any type of job could have accessibility challenges.
4. Contractors May Charge More For Projects With Specific Safety Requirements.
Some projects have safety requirements or building codes that require additional specialized equipment and impact the time it takes to do the job.
Safety requirements are associated with more complex or commercial jobs. If your project is residential, this factor likely will not apply to your quote.
5. Contractors May Charge Separately For Labor.
Some spray foam quotes may break down labor cost, while others do not list man-hours. Contractors must consider this factor, whether a quote references man-hours or not.
How labor costs influence your quote will vary by contractor. Even contractors who include their man-hours in their spray foam rates may separately charge for prep work or existing insulation removal.
6. Contractors May Charge For Travel Time.
Travel time is a factor that will vary by location and market.
For example, let's say you live in an area with several contractors within reasonable driving distance. These contractors may not include travel time in their quotes.
However, if the closest contractor to you is someone over four hours away, travel time may become a factor in their quote.
At South Central Services, our service area extends about 45 miles from Greencastle, Pennsylvania in every direction. As long as the project is located within our service area, we do not charge additionally for travel time.
7. Qualified Contractors Know How Much Effective Spray Foam Costs.
Not every contractor with a spray foam rig is well-trained or qualified. A knowledgeable and qualified contractor should charge the amount it will take to do the job right. In many cases, contractors with higher bids are demonstrating their expertise by not undervaluing the cost of the job.
However, it is not as simple as saying the highest quote means the most expertise. Higher quotes may come from contractors with more expertise. However, it is not a rule that the highest quote equals the greatest expertise.
Contractor expertise may be a factor that influences the cost of spray foam, but price cannot be the only factor influencing your choice of contractor.
You cannot choose a contractor solely based on price. It is vital to work with a company and contractor you trust, regardless of their quote amount.
The Bottom Line About Why Spray Foam Insulation Is So Expensive
Many factors contribute to the price of spray foam insulation. Not only is spray foam a premium product with higher manufacturing costs, but the details of every installation can impact the final price. Whether your project is a straightforward installation or a more complex job, you must work with a contractor who will deliver a high-quality finished product.
Now that you know why spray foam insulation is so expensive, your next step is to:
- Calculate an estimate of spray foam for your project
- Determine if spray foam is worth investing in for your current home
- Learn how to save money on spray foam using a federal tax credit
Disclaimer: While we strive to publish information accurate to building science, local building codes and standards supersede our recommendations.
Alexis has been fascinated by spray foam insulation since 2018. When she isn’t thinking about insulation, Alexis is geeking out over storytelling and spreadsheets.
Topics: