Can Houses Be Sealed Too Tight? An Examination In Building Science
May 7th, 2025
4 min read
By Kilian Agha
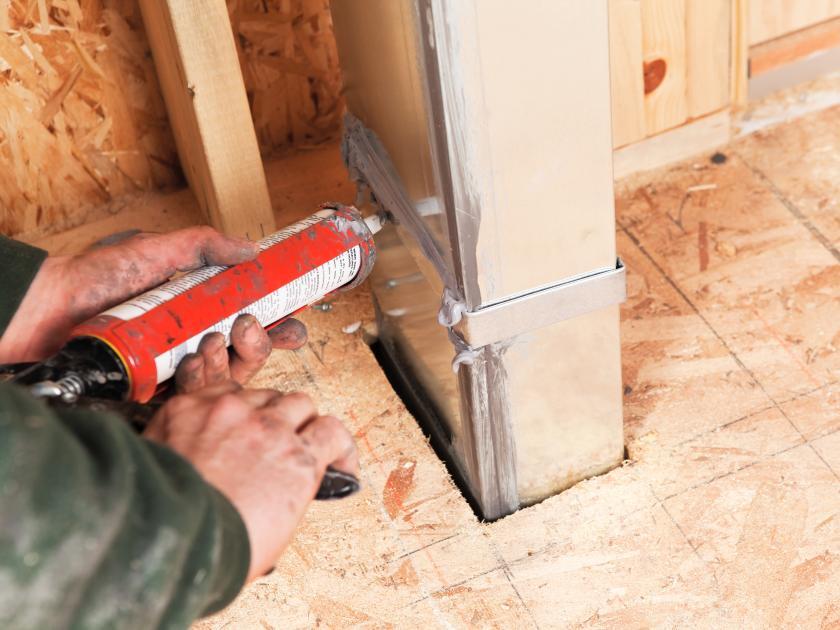
We often get pushback about air-sealing and spray foam insulation. Builders who have been in construction for decades have concerns about stopping ventilation in building assemblies. Rightfully so. You may have never seen or heard objective evidence favoring this new building style.
This article will break down the concept of air-sealing and examine evidence supporting sealing up a house tightly. You'll also have access to case study files to examine.
By the end, you should be equipped with:
- The principle behind air-sealing
- Evidence for air-sealing success
- Caveats when air-sealing a building
The Principle Of Air-Sealing.
Air-sealing aims to prevent as much random air infiltration as possible. In traditional construction, homes are left open to natural ventilation. Air can pass through the building assemblies. Before more sophisticated mechanical ventilation, this natural ventilation was vital to ensure fresh air entered the home.
Air-sealing proposes that random air infiltration does more harm than good in modern construction. While natural ventilation in the building assemblies does allow fresh air exchange, it also causes the following:
- Hotter homes in summer
- Colder homes in winter
- Strain on HVAC equipment
- Drafts
- Moisture problems
Uncontrolled air has unidentified quality, as well. The infiltrating air could be clean. However, it could also include pollution and VOCs. There is no way to measure or purify the air that leaks into the home.
As building science has advanced, building an energy-efficient home has become more important. Evidence shows that the most efficient homes utilize mechanical systems and prevent as many air changes per hour (ACH) as possible. Building standards continue to shift towards low ACH to pass inspection.
The Evidence For Air-Sealing.
The following sections will summarize case studies in favor of air-sealing. Each section will also include a link to the original source so that you can examine the evidence firsthand.
Study: American Council for an Energy-Efficient Economy (2014).
This case study was conducted in Oregon. The first test was completed in 2012, and the second in 2014. The study aimed to measure air-sealing's impact on ACH when applied to specific aspects of construction.
The first test examined the use of a foam gasket on the top plate of the walls. This simple and cost-effective method cut ACH by 0.8 in these homes compared to untreated homes. Expressed in another way, air leakage was reduced by 15% with treatment.
The second test examined the use of blown-in insulation in wall systems. The average ACH delta between untreated and treated homes was approximately 1 ACH.
Both tests in this case study applied air-sealing methods to a small area of home construction and successfully lowered the number of air exchanges per hour in these homes.
This American Council for an Energy-Efficient Economy case study is 14 pages long and available as a PDF.
Study: U.S. Department of Energy (2014).
This case study was conducted on Minnesota homes. The testing began in 2012, and the study was published in 2014. This case study was designed to examine the impact of airtightness in a roof system in cold climates.
Ice damming on the roof is a significant concern in cold and frigid climates. The goal was to examine the effectiveness of roof-only air-sealing related to thermal and air control layers.
This study examined five methods that spanned five unique homes. The methods (Page 10) included:
- 6 inches of fiberglass faced isocyanurate installed over roof decking
- 2 inches of closed cell spray foam at base of rafter cavities with 6 inches of ISO rigid insulation over roof decking
- Closed cell spray foam and blown-in cellulose
- 2 inches of polyiso (3 layers each) on top of roof sheathing with 5 inches of dense pack cellulose in the rafters
- 1.5 inches of polyisocyanurate between rafters and spray foam in rafter bays
Many conclusions were drawn, but one important takeaway is that the most improvement in air leakage reduction came from whole-house air-sealing efforts in two of the five homes.
This U.S. Department of Energy case study is 50 pages long with many pictures and diagrams. It is available as a PDF.
Study: Air Infiltration and Ventilation Centre (2022).
This case study examined data from 1,700 homes across the United States that received retrofit air-sealing for the attic, home envelope, and ductwork. Unfortunately, attic air-sealing was "rare and insufficiently documented" (Page 4) for this study, so much of the findings focus on envelope and duct sealing.
The study found that both types of air-sealing reduced air leakage, with duct sealing being more effective. This case study also examined costs related to the outcomes. This study is 7 pages long and available as a PDF.
Study: U.S. Department of Energy (2012).
This case study examined data from a large multiunit building complex retrofit project in North Carolina.
The retrofitted buildings included townhomes and apartments. Common air leakage that was sealed during this project included:
- Sealing duct boots to subfloor
- Repairing openings in ceilings
- Patching around plumbing repairs
- Sealing windowsills with caulking
- Sealing gaps and penetrations with foam
Total unit enclosure leakage was reduced on average by 50%. Based on this and other testing, the study found major leakage problems in the electrical and plumbing penetrations, dropped ceilings, ductwork, floor-to-wall intersections, and windows.
The study modeled possible energy savings due to these retrofit air-sealing efforts. Some of their conclusions about savings were as follows:
“Modeling of the estimated 50% leakage to outside reduction at the test site yields a 15% to 25% reduction in space conditioning costs, or a 3% to 15% reduction in overall energy expenditure, with a payback period of 1.4–12.2 years, depending on climate location.” (Page 24).
This study is 54 pages long and available as a PDF.
The Conditions When Air-Sealing.
In the 2022 case study from the Air Infiltration and Ventilation Centre, the need for mechanical ventilation when air-sealing was clearly identified:
“Mechanical ventilation is an important element of energy retrofits that reduce air leakage. In order to dilute or remove contaminants of indoor origin it is necessary to maintain minimum ventilation flows and use local exhausts in kitchens and bathrooms.” (Page 5)
In this study, a lack of mechanical ventilation was identified:
“Unfortunately, we found that provision of adequate ventilation was rare and requires additional emphasis or mandated requirements in future programs to ensure that indoor air quality (IAQ) is not compromised in decarbonized, energy efficient homes.” (Page 6)
When we advocate for sealing up a house very tightly, we must also advocate for appropriate mechanical ventilation. Homes do need ventilation. It is vital to preserve indoor air quality. An air-sealed home with appropriate mechanical ventilation will net better energy efficiency and air quality.
Air-sealed homes can offer better performance than traditional homes, but the insulation and HVAC must work together to create that result. Sealing a house without proper ventilation would be foolish and unsafe for the inhabitants.
Homes Cannot Be Sealed Too Tight, According To Building Science.
In all of these studies spanning 2012 to 2022, no researcher argues that homes can be sealed too tightly. Rather, these scientists aim to find the most effective and efficient methods for air-sealing in their climate zones. The cost-effectiveness of air-sealing is sometimes examined, but the usefulness of air-sealing for energy efficiency is not in doubt.
However, it is also vital to acknowledge the need for mechanical ventilation in the case of air-sealing. The need to mechanically remove indoor air pollution increases when ACH is lowered for energy efficiency.
There is no harm to the construction of a home when it is air-sealed. The greatest concerns with air-sealing are methods and appropriate HVAC equipment to support the inhabitants.
Kilian has co-owned and operated South Central Services for 8 years. He is passionate about community involvement. In his spare time, he enjoys being with his family, playing ice hockey, and going fishing with friends.
Topics: